Solid Polycarbonate Sheet
SME PC sheet is made by pure 100% PC raw materials from a well-known foreign manufacturer (Bayer/Germany)/US GE/Japan Mitsubishi), made in Taiwan.
SME PC sheet has several characteristics such as impact resistance, light weight, and easy processing, so that the product can be widely used in buildings such as roof skylights, window canopies, advertising billboards or other decorative applications.
Description
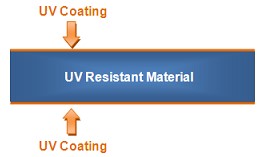
Solid Polycarbonate Sheet Specifications
• Impact strength: Solid PC sheet is 200 times harder than glass. Therefore, it can be used as a safe construction material.
• Light weight: The weight of PC Solid Sheet is only about half of glass.
• UV-protection: PC sheet is co-extruded with a high-density ultra violet ray absorbent to fight against ultra violet ray, it can prevent yellowish and frailness.
• Weather resistance: PC sheet remain cool and suitable temperature from it's UV protection.
• Sound insulation: The polycarbonate resin offers significant advantage to the sound insulation and it can also be used in soundproof.
Solid Polycarbonate Sheet Applications
• Steel processing facilities (especially under thermal bending) in installation architecture.
• Roof light in office buildings, department stores, gymnasia, hotels , fast-Food restaurants, churches and hospital etc...
• Archshaped dome skylight in parking lots, shopping mall, swimming pool, supermarket and atrium etc...
• Display cabinet in police office, gatehouse, jewelry shop, gas station, tollbooth, bank, and luxury watch shop etc…
• Light cover or roofing of warehouse, factory, and greenhouse, and garage awning.
• Interior decoration like ceiling, light box, and office compartment.
Related Applications
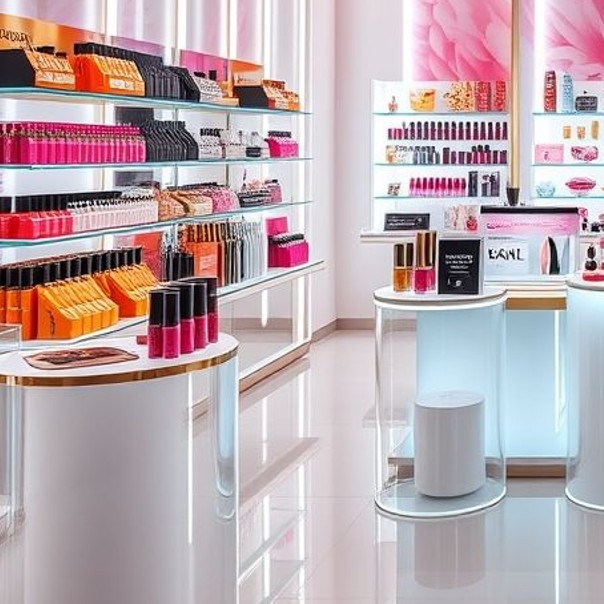
-1.jpg)
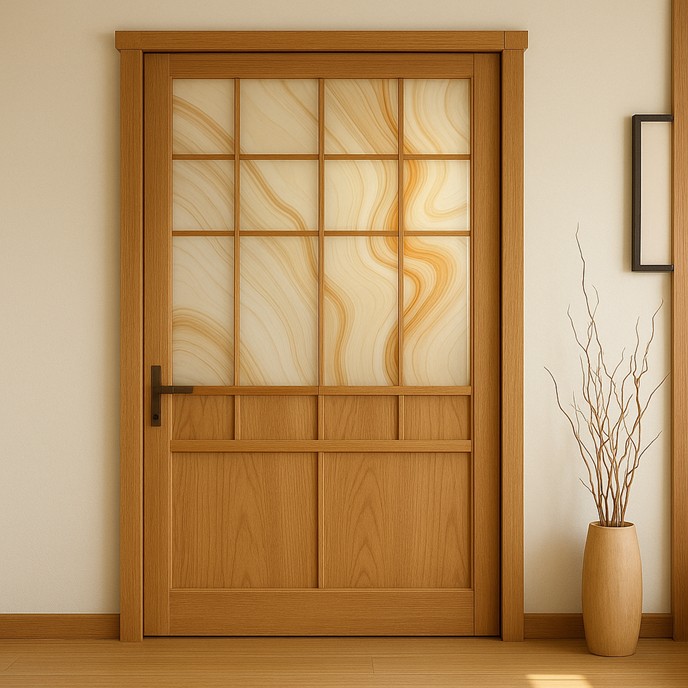
.jpg)
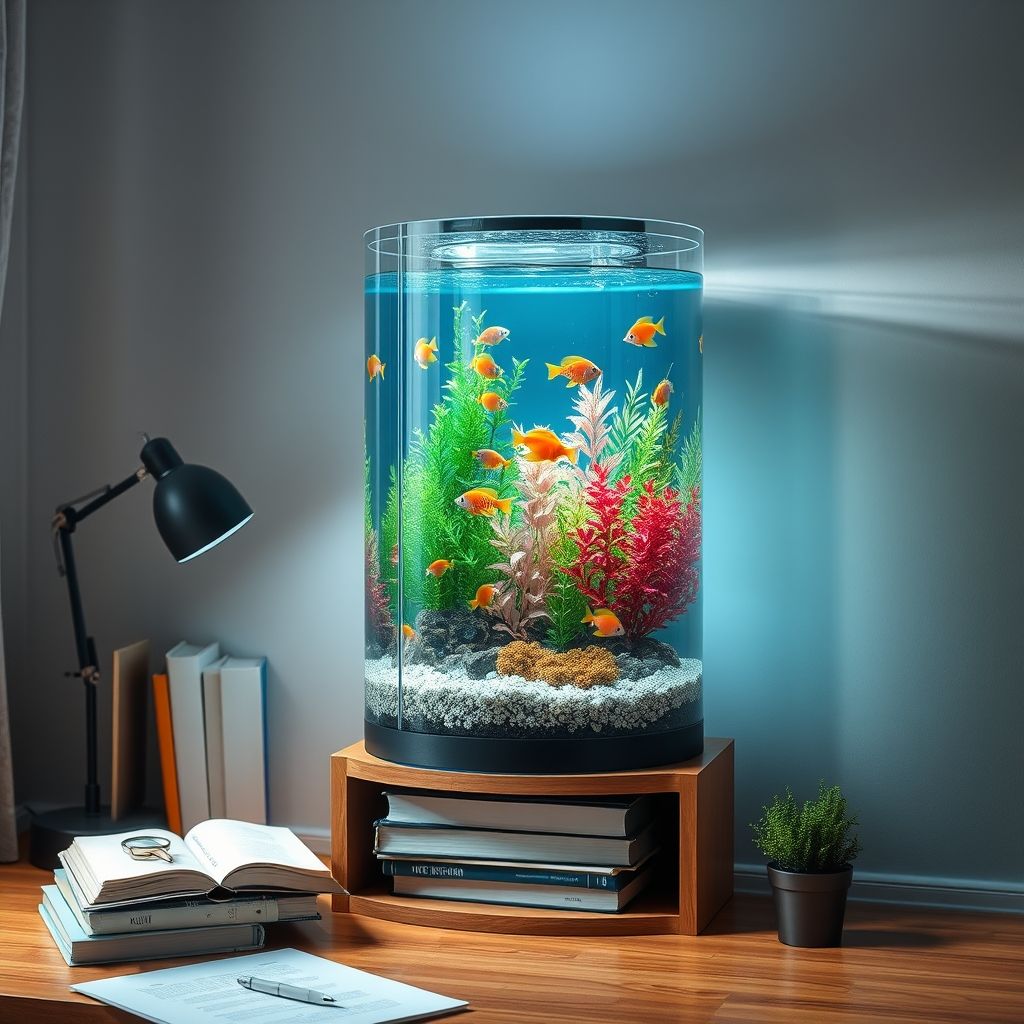

- Cutting: Cutting according to the size required by customers, the precision tolerance can reach ±0.5mm
- Polishing: Treat the acrylic surface with a diamond polishing machine to make it smooth and translucent.
- Drilling: Drilling according to customer's requirements, and it is matched with customer's sample kit.
- Bending: Bending according to customer's requirements, heating the acrylic tube, and then bending with jigs.
- Chamfering: The edge of the acrylic pipe is chamfered to reduce sharp edges.
- Printing: Print patterns, words or images onto the acrylic surface to achieve personalized decorative effects.
- Laser cutting: Using high-power laser beams for precise cutting can achieve diverse cutting needs.
- Assembly: process and assemble with the accessories required by customers to complete one continuous line service.
- SMEACRYLIC® is a Taiwan based manufacturer which was founded in year 1980, a Professional Manufacturer in Extrusion Technology.
- We specializes in extruding various kinds of plastic Profiles, Tubes, Rods and Sheets which be used in displays, decorations, lighting, illuminated advertising, architectures and a lot more applications.
- Approximately 90% of our products are exported to over 40 countries worldwide including numerous well-known brands. Over the years, we have expanded to become the market leader in extrusion field in Asia.
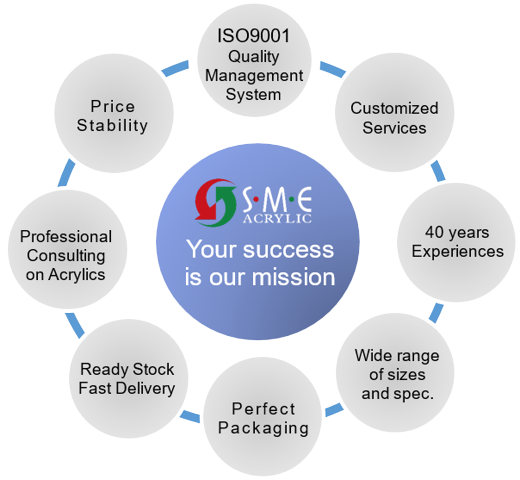
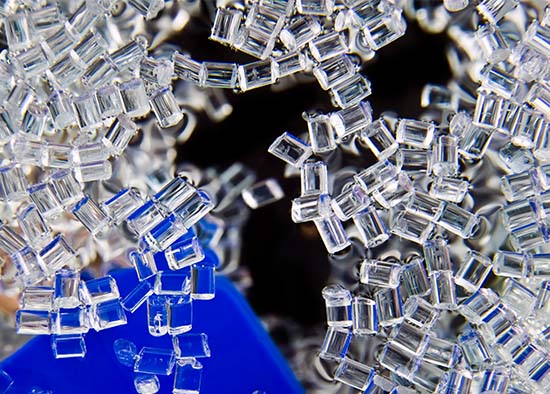
We insist on using 100% virgin materials.
We insist on using international branded raw materials (Sumipex, Mitsubishi, Evonik)
We insist on keeping sample records of raw materials, all raw materials are traceable.
- We developed on line catalogue for our customers.
- Stock system always offers efficient prompt delivery.
- Samples available for most of our products.
- Our home-made moulds offer fast and precision work to ensure customers' satisfaction.
- Efficient ISO-9001 managing system ensures quality stability.
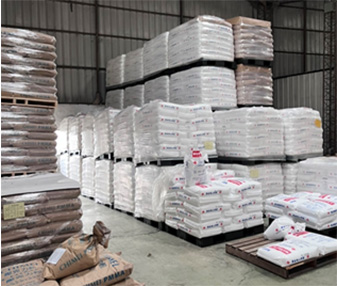
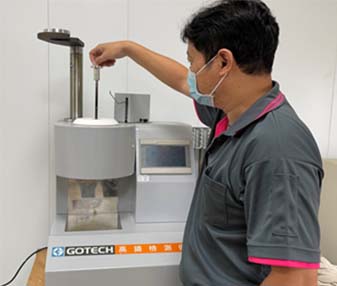
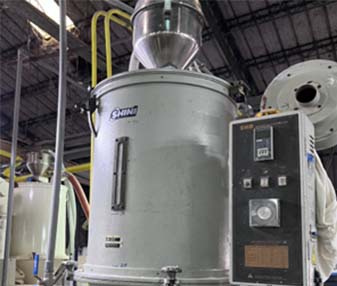
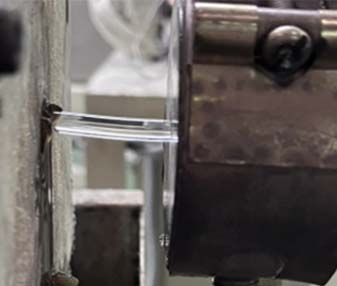
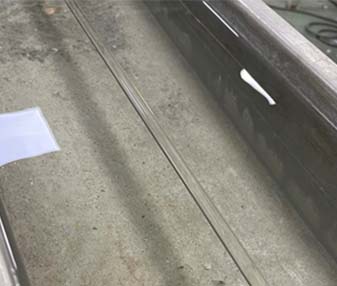
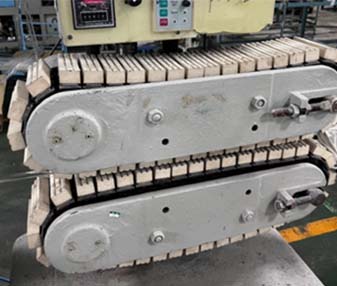
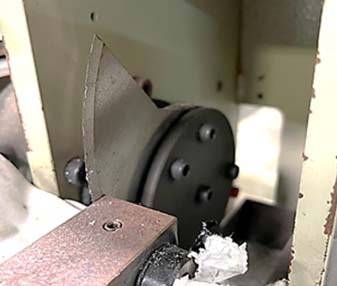
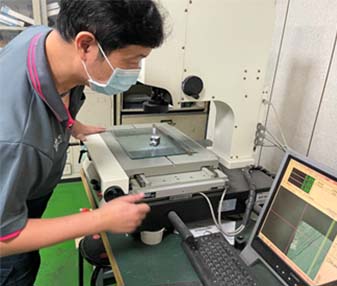
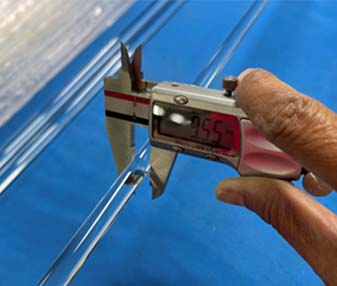
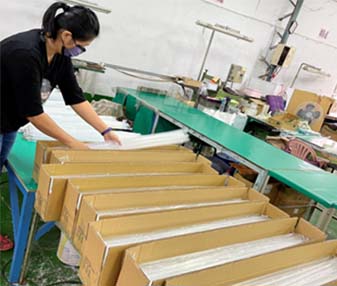
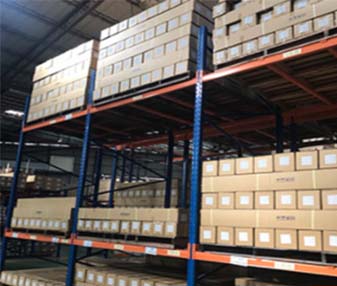
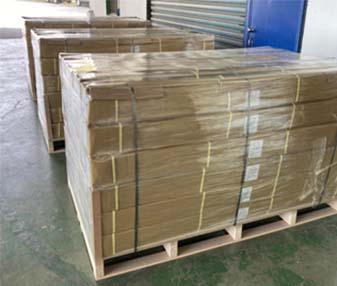
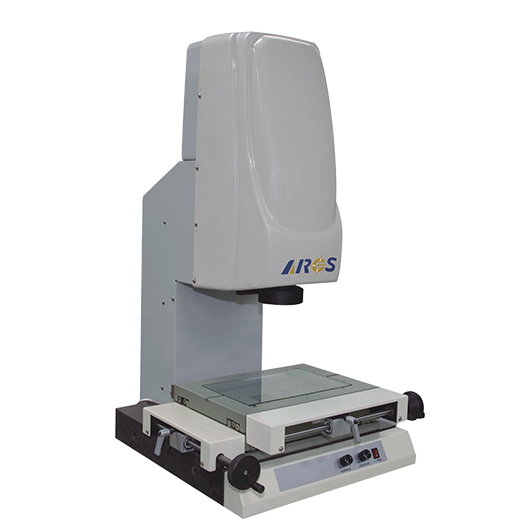
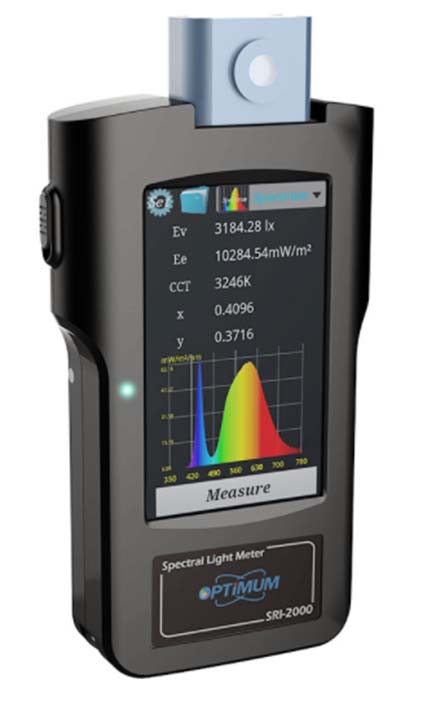
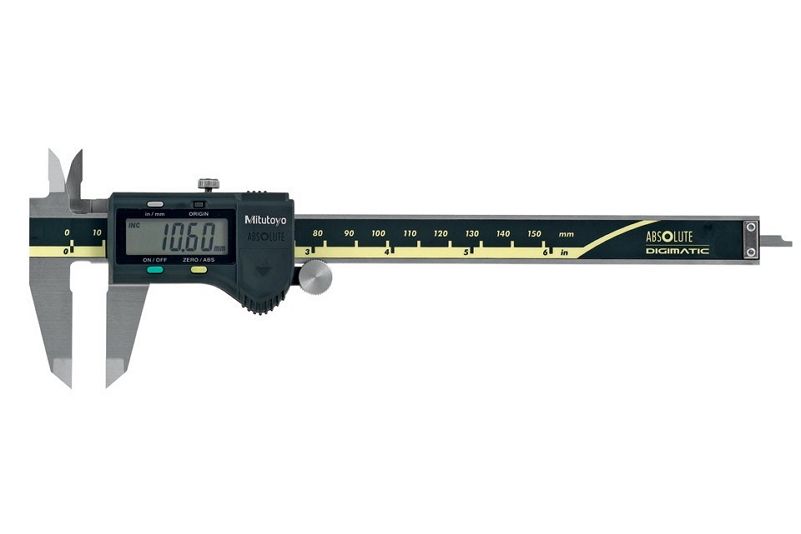
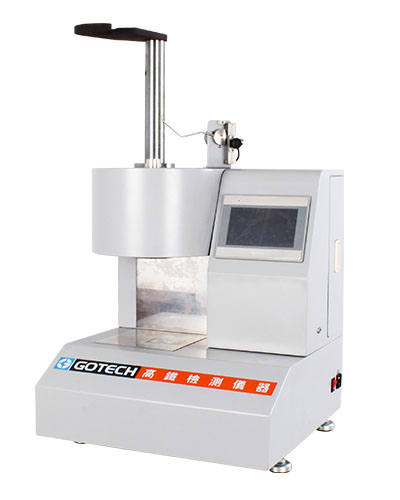
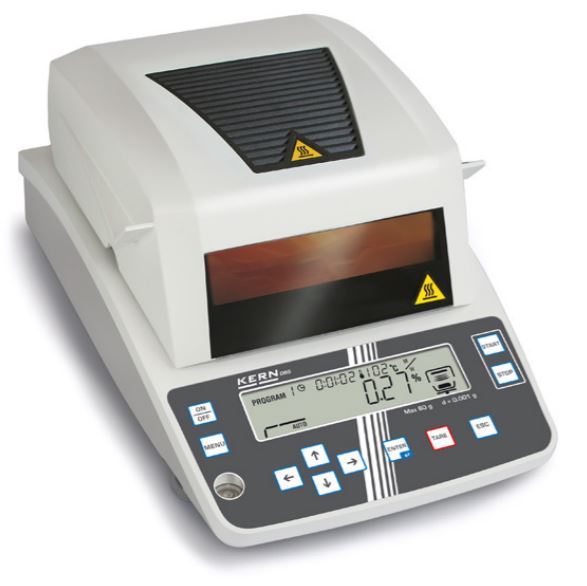
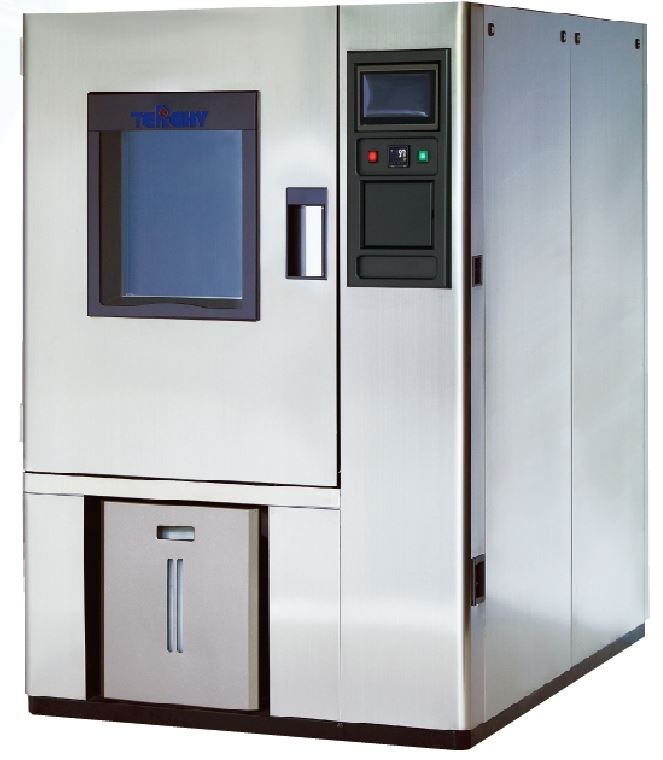
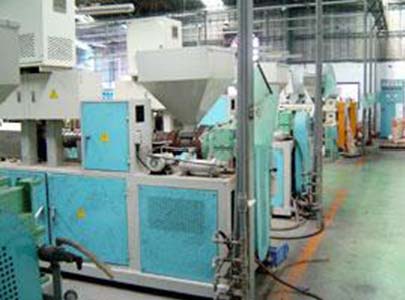
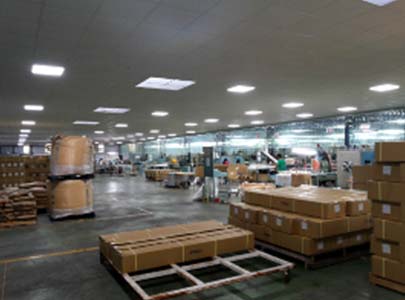
- Exclusive shrink film packaging slows down the water absorption of acrylic
- Giving you a good cutting experience
- Effectively avoid scratches on acrylic tube surface during cutting
- Small tubes are bundled to increase the strength and are not easy to break
- Bubble Wrap protects the tubes druing transportation
- Carton protection, convenient for warehouse management
- Square package, maximizing the storage capacity of the warehouse

