Acrylic Curtain Blind Rod
SME’s acrylic curtain rods can produce various shapes according to customer needs, including circle pull rods, hexagonal rods, star-shaped tubes, fan rods... etc. At present, Acrylic Curtain Blind Rod has cooperated with nearly 10 domestic curtain manufacturers.
Description
Acrylic Curtain Blind Rod Features
• Processing guide circle and assembling hardware parts.
• If you have a new design, please provide drawings to us.
• Please click here to see the specifications of our Acrylic Curtain Blind Rod.

- Cutting: Cutting according to the size required by customers, the precision tolerance can reach ±0.5mm
- Polishing: Treat the acrylic surface with a diamond polishing machine to make it smooth and translucent.
- Drilling: Drilling according to customer's requirements, and it is matched with customer's sample kit.
- Bending: Bending according to customer's requirements, heating the acrylic tube, and then bending with jigs.
- Chamfering: The edge of the acrylic pipe is chamfered to reduce sharp edges.
- Printing: Print patterns, words or images onto the acrylic surface to achieve personalized decorative effects.
- Laser cutting: Using high-power laser beams for precise cutting can achieve diverse cutting needs.
- Assembly: process and assemble with the accessories required by customers to complete one continuous line service.
- SMEACRYLIC® is a Taiwan based manufacturer which was founded in year 1980, a Professional Manufacturer in Extrusion Technology.
- We specializes in extruding various kinds of plastic Profiles, Tubes, Rods and Sheets which be used in displays, decorations, lighting, illuminated advertising, architectures and a lot more applications.
- Approximately 90% of our products are exported to over 40 countries worldwide including numerous well-known brands. Over the years, we have expanded to become the market leader in extrusion field in Asia.
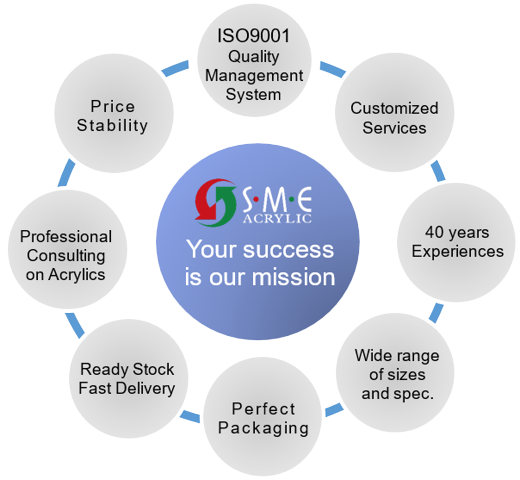
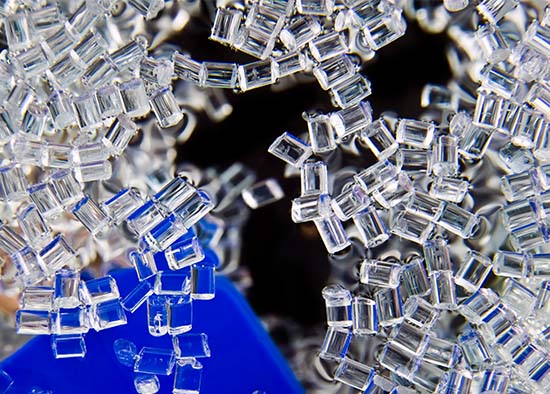
We insist on using 100% virgin materials.
We insist on using international branded raw materials (Sumipex, Mitsubishi, Evonik)
We insist on keeping sample records of raw materials, all raw materials are traceable.
- We developed on line catalogue for our customers.
- Stock system always offers efficient prompt delivery.
- Samples available for most of our products.
- Our home-made moulds offer fast and precision work to ensure customers' satisfaction.
- Efficient ISO-9001 managing system ensures quality stability.
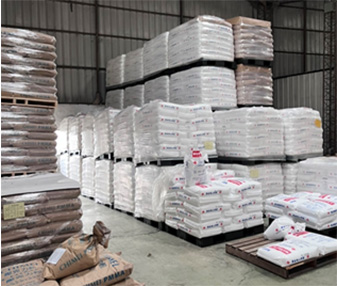
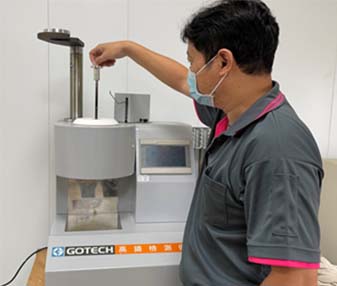
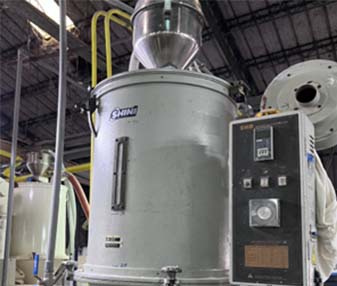
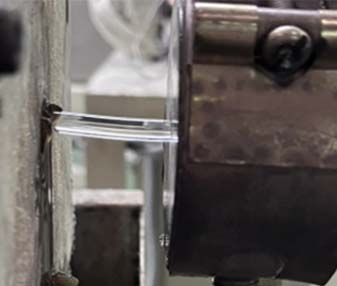
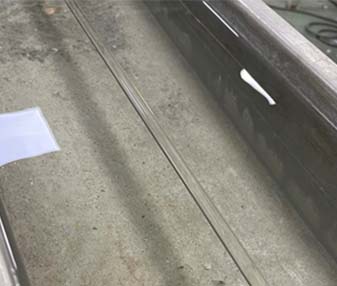
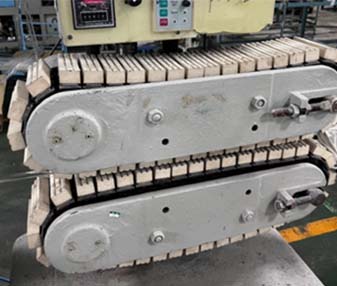
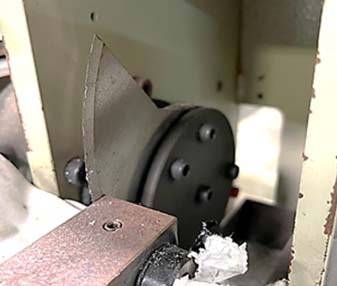
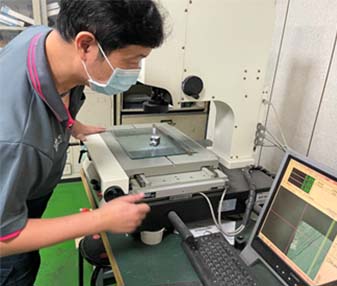
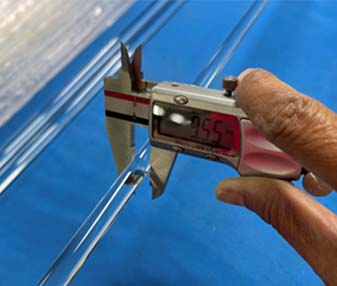
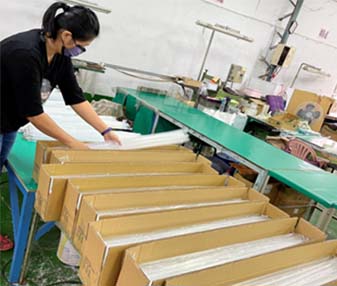
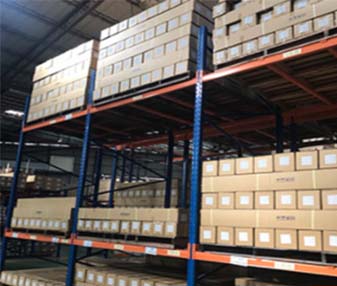
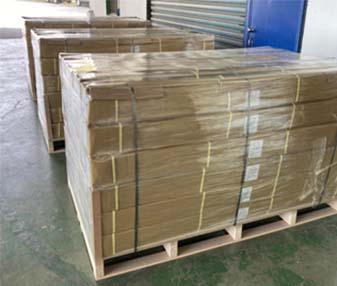
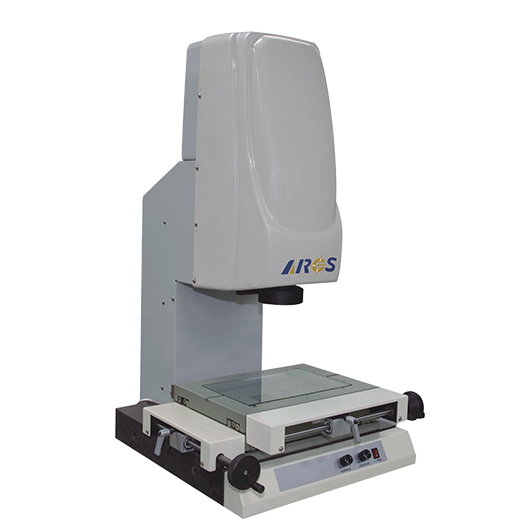
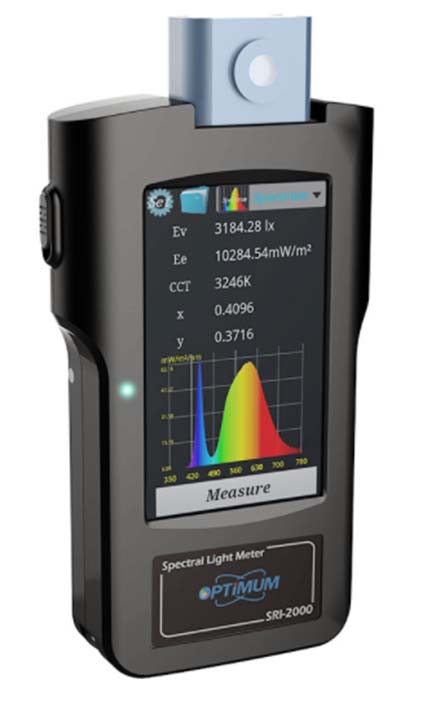
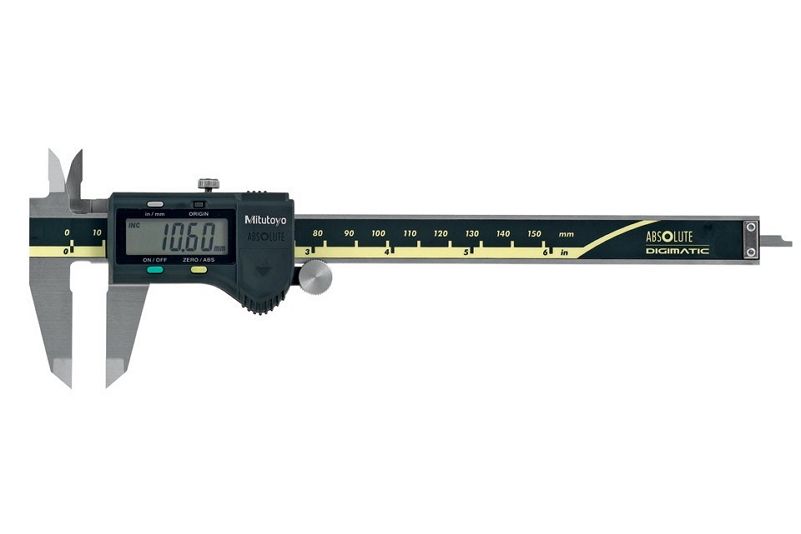
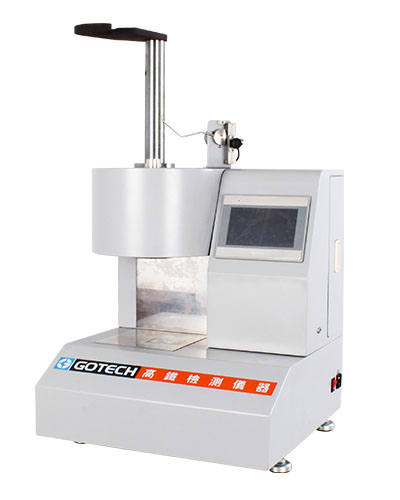
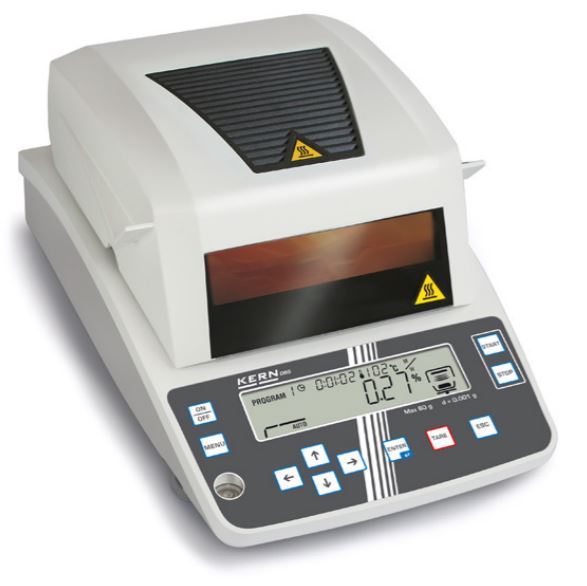
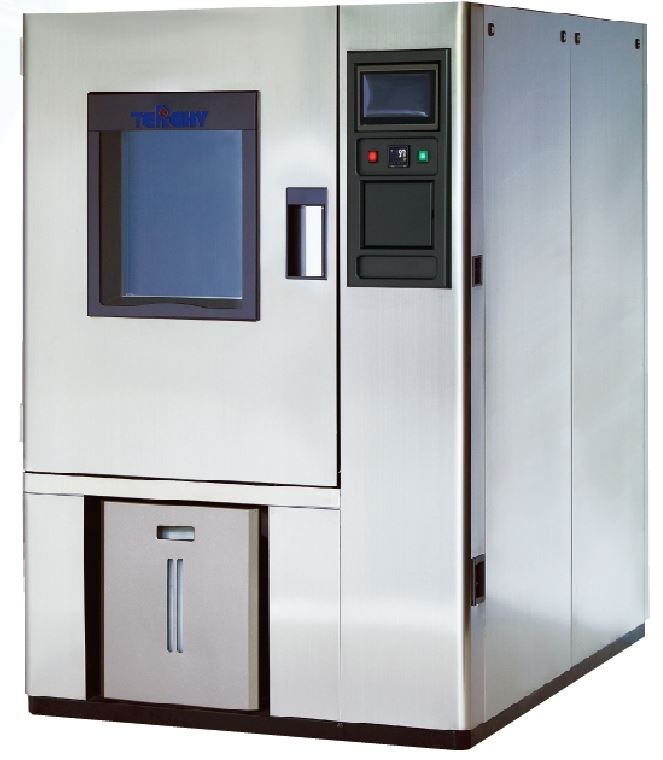
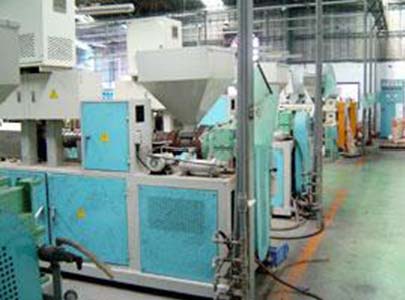
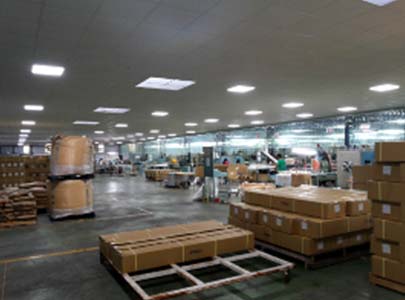
- Exclusive shrink film packaging slows down the water absorption of acrylic
- Giving you a good cutting experience
- Effectively avoid scratches on acrylic tube surface during cutting
- Small tubes are bundled to increase the strength and are not easy to break
- Bubble Wrap protects the tubes druing transportation
- Carton protection, convenient for warehouse management
- Square package, maximizing the storage capacity of the warehouse

